Anti-didymo spray
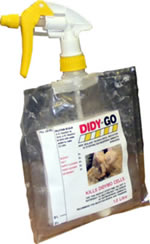
Kyle Van de Pas
St John's College
Year 12 Materials Technology: full year project
Teacher: Steve Andrew
In Year 11 Kyle made an indoor non-ice curling stone – see his previous Student Showcase. In his Year 12 Materials Technology course, he wanted to do something different. "I wanted a project where I had to solve a real problem – an important issue that I could spend some time working on."
The issue Kyle settled on could not have been more real, nor more important – he decided to see if he could do something to reduce the spread of didymo in New Zealand waterways.
Kyle began by finding out about the problem and identifying the stakeholder groups. "I found out which waterways were contaminated, and the human activities that could spread the weed. I originally thought I'd do something with boats, but the contaminated waterways tended to be in alpine areas and there's not that many boats going up there. So I focussed on mountain bikers and trampers and the gear they carry with them that gets wet to identify what needed cleaning after they went through a waterway. I also had to figure out how to kill the didymo."
Kyle decided to develop a product that could be carried and used to kill off didymo on tramping and mountain bike equipment. His final brief included specific user group specifications for the product – it would have to be small and compact and easy to use in the environment they were moving in.
Kyle carried out a detailed analysis of a range of existing products such as camping showers, squirter bottles and car wash wipes which he might be able to adapt. "I had concepts of things like a hot water bottle with a big opening that would get the solution quickly on your gear – but that would mean a lot of waste. Using the camping shower idea with a long hose would let you direct the solution onto specific parts. Then I thought of the spray gun approach – using a bag that you could roll up when you've finished and save on the space. That would be easy to use to direct the spray on to your boots, say, without wasting too much. I also looked at using different materials for the bag to stop it ripping, but found that the cost of a bag can be so small that it would be easier to be disposable."
Kyle worked with mentors from NIWA and a local manufacturing company Convex Plastics who helped him to evaluate his ideas. "I asked NIWA if it would be possible use the water from the stream to dilute the solution. They told me that it wasn't ideal but that it would work. That solved the space problem – the mixture I was using was a 5% solution, so that reduced the amount of liquid to be carried by 95%.
Kyle then developed a range of mock-ups and models, which he tested with the user group. This showed him what would work well for them and enabled him to settle on a final concept for development through to the prototype stage.
"The product I've come up with is unique in that there's nothing out there yet which is doing the same thing. I've taken two existing ideas – the spray bottle and the plastic bag – and made a spray bag."
"My biggest decision was how to attach the spray gun to the bag. There needed to be a thread on the bag, and that's quite hard to do. When I talked with Convex Plastics they gave me another idea that I developed up –putting a lip on the spray gun so the bag could be secured onto the lip with a band or a clip. That would help with the manufacture but made things trickier for the users and might put them off using it."
Kyle decided that ease of use was vital and that using a thread was the best solution, although this meant that the product could only be economically manufactured in bulk overseas.
"Scientists have put a lot of effort into stuff that will kill the Didymo – but nobody has really been looking at how that stuff can be effectively used. Now I've got a product that can be used and the labelling to show people how it can be used properly."
His labelling incorporates a dilution scale that shows how to mix the various solutions used. He finished the prototype development by designing and constructing a display unit to be used to promote the product in a shop.
Kyle particularly enjoyed working with plastic as a construction material. "It's a material that I haven't really used much before and getting the chance to work with a company like Convex Plastics let me see how its made and how a plastics factory operates. Also, learning how a simple machine can be used to manufacture my product and seeing it all happening has been cool."