Custom classroom furniture
BODYFURN SIDE STORAGE UNIT
Manufacturing
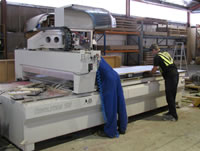
Cutting and drilling of the panels is done automatically by computer-controlled cutters on a large flat-bed machine. (Click to enlarge)
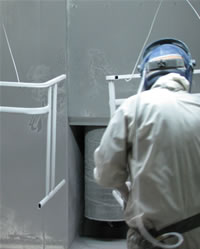
Powder coating is done at the Furnware factory – a dry powder is sprayed alongside the unit and is attracted on to the surfaces using electrostatic forces.
(Click to enlarge)
By the time manufacturing of the side storage units began, Furnware had already sold 1,000 units. Normally the company would do a trial production, but they had already trialled 30 test samples in a classroom. "Because of the process we'd gone through, we were extremely confident with what we had, so we went ahead and made that first 1,000 units," said Steve.
Standard production time for Furnware products is three weeks, as the company needs time to: process the orders; order in materials, some of which has a long lead time (the MDF for the desks has a five day turn-around); do any drawings/plans of special items; a five day cycle of production from machining to assembly; and then dispatch. However, the manufacturing time for a side storage unit is literally a day or less, as it's only a matter of minutes to put one together and screw it to a desk.
Furnware orders the components in lots of 500 – the plastic ones from Axiam and the steel from a local company that laser-cuts and folds the steel. The only in-house manufacturing is the powder-coating of the steel – which can be done in lots of between 100 and 500 units – and assembly.
To ensure that they do not run out of components, the factory uses a kanban system. The kanban (Japanese: literally 'visual card') system is a card inventory system used in manufacturing plants to ensure a continuous supply of components while minimising overstocking. The system was first introduced by Toyota in their main plant machine shop in 1953. At Furnware, trolleys are used, each of which holds 60 units – whenever they are half empty they are replenished.
The Furnware factory itself normally runs on a 10-day production turn-around. Twice a day – at 8am and 12 noon – orders come from the front office to the leader of the production team who does the production planning. The production team works through these orders within the four-hour period to produce the Bill of Materials, which lists the costings for materials and labour and methods of assembly and dispatch.
An information sheet listing the jobs to be placed is sent to the planner, who plans the next appropriate time for the jobs to be done within the following ten days. About three to four days before the assembly date, the job will start to be machined or assembled. Two teams – the steel department and the panel department – have a daily link that makes sure that they're both on track, so that the product arrives back to the production team leader on the day that he designated, so that it can be assembled on the due date.
"Things can be done quicker than ten days," said Steve, "but that may mean taking something out of our plan if we have a fully loaded workshop. However, if there are gaps, it's quite easy to fit something in. If I needed Bodyfurn chairs dispatched quickly, there's no reason why I couldn't place an order at 10am and have them dispatched at 10am the next day if I really had to – our robots can punch out 100 items a day. This is because we have a lot of plastic in stock – we order them in lots of 1,000."
"The only thing that holds us up is the desktop material – we don't keep any in stock as the we have a kanban system agreed with the manufacturer, which means we carry a lot less stock and that saves us – and ultimately the customer – a lot of money.