Custom classroom furniture
BODYFURN SIDE STORAGE UNIT
Production planning
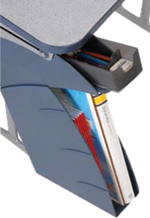
The next stage for Furnware was deciding how to manufacture the unit efficiently. Getting a prototype to the final manufactured product is a big responsibility said Steve.
"At this point you start investing time and money into materials. If you're still just talking, things it can be changed quite easily, whereas from now on, if you get it wrong, there's a large cost. And that's my responsibility – I'm the one that has to say 'Yes we should move with this tool'."
Generally Furnware products are made on-site, mostly from raw materials such as tubular steel and MDF. The only outsourced manufactured items are the general assembly components such as wheels, castors, plastic plugs and hinges, and commissioned injection-moulded plastic items for seat shells and the side storage unit.
PRODUCTION
People/Labour
- Availability of skills required
- Production time per unit
- Assembly time per unit
- Packaging and dispatch time
Tooling
- Major tools to be built
- Templates
- Jigs
- Special tools, e.g. for assembly
Other resources
- Processing capabilities, e.g. painting or powder coating
- Factory space
Outsourcing
- Can someone else do parts of the process for us?
Costs
- Can we keep the total cost within the target?
- How many sales are required to recover the development cost?
- How long will it take to recover the costs?
Furnware contracted Wanganui company Axiam to injection-mould the plastic components which make up the side storage unit, and they were involved in the decision-making and design of the tools to make them.
"Once Murray had done his first conceptual design and we'd ironed out the issues and got all the little additional pieces put into it – like the clip and the release mechanism – we got Axiam to run through and to look at plastics. They gave us good feedback on our design moulds and costs etc. Part of the role was to help us with information about designing tools, shrinkage of plastics, and which materials would best suit us. A lot of time was spent going back and forward using Murray's 3D models, with Axiam's involvement about how it would effect their tooling and the size of their machines, etc, until we got to the point of signing off on the manufacture of the tools."
"For manufacturing, we looked at splitting the top half of the box in two and realised that we had potential to make the box slide in. This was desirable, but there was an extra cost – an extra tool, assembly time, screws, etc. We went back and analysed it and Murray came up with an idea where he castellated parts of the injection moulding tool we were designing, which gave us a simple solution for what we wanted and saved us a lot of tooling money.
Steve went to Axiam's Wanganui factory to help test and fine tune it. "For example, we'd calculated the energy required to snap off the box, but when I tested the clip, the box came off too easily. So I spent a few days going through the method to fine-tune the tool so it made the clip strong enough. I also went through some production issues, like how to get rid of the little sprag that gets left in the tool."
Steve said these sorts of issues occur in every new job and some don't become apparent until you've started working with the materials.
"For example the handle was made of the same material as the rest of the unit, but it was giving us too much flex and didn't look strong enough, and the clips weren't rigid enough. So we ended up changing the material and added a component of glass-filled nylon to the clips. This caused another issue: the shrinkage factor of glass-filled nylon is less than the plastic. So we then had to make a modification to the tool to allow for this lack of shrinkage."