THE HERB FARM REVISITED
The production manager role
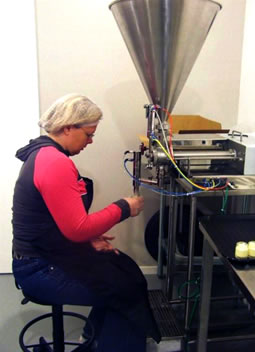
Nicola at the filling machine
With ongoing development of the product range, a growing market demand and a newly established dedicated manufacturing unit, the time was right to increase staffing in the manufacturing area.
Nicola Walker joined the Herb Farm team as production manager in 2008, and has already proved herself to be a vital component of The Herb Farm's successful expansion and streamlining. Although her background is in the manufacturing side of the dairy industry, Nicola has always had an interest in natural therapies including herbal studies and homeopathy. Locally born and bred, Nicola leaped at the chance to come back to the Manawatu to do something she felt really passionate about.
"The role gave me the opportunity to get back into natural therapies and do something wonderful for the environment and for people. It was just a case of following the heart really," she says.
Nicola's role is to plan and coordinate the production of The Herb Farm's product range. She works within monthly and then weekly timeframes, generally focussing her production schedule on shop sales and orders received from retailers each month and managing the materials used and the time needed in the manufacturing room to get the most efficient use of the available resources.
As the production manager, Nicola has to be totally hands-on in the manufacturing unit. An important part of her position is to make sure that every new batch of The Herb Farm product is as good as the last, and that they are always well stocked to meet the demands of retailers and personal customers.
"Being a production manager requires you to be flexible and look at the whole process – you've got responsibility for the whole thing not just a small part of it," she says. "You have to be able to solve problems at any stage in the process and have the confidence to make judgment calls and to communicate effectively with other people when you need to. It's a really varied role – you have to be able to multi-task and look outside the square a bit. Working in production is far from being routine – when everything is going well it might look that way, but it's not always like that and you've got to be continually thinking on your feet."
The batch production process
Before making a new batch of a product, Nicola first matches current stock levels with actual and likely future demands. From this information she makes a production schedule that outlines what needs to be done for the coming week. Although she likes to keep to the plan Nicola knows that there has to be some flexibility as special orders often come through. "We've got one at the moment for 500g of a foot balm," she says. It's a one-off order and I need to make sure that it can be scheduled in and done as quickly as possible."
Once a product comes up on the schedule, Nicola refers to its formulation sheet – a print-out of the process, with all the necessary ingredients and detailed instructions on how it is manufactured.
From there, ingredients are taken through to the manufacturing area where the initial stages of production happen – wiping down the benches, preparing the equipment and weighing out the amounts needed following the batch recipe. Generally each batch size is about 5-6kg and makes about 100 jars.
The first step in the process is mixing and emulsifying the ingredients, which is done in the jacketed pan – a vessel with hollow steam-filled walls and an internal agitator that enables even, controllable heat transfer to its contents. "For most products it requires about 25 minutes in the jacketed pan. The pan melts things and mixes them up, and then we cool it all down and carry out the blending process. We generally do three blends of about 45 seconds each with five minutes in between for cooling."
The third blend (after 15-20 minutes) tends to be where the heat-sensitive ingredients, such as essential oils, are added to the mix, before the product is left to fully cool. Generally this takes a day but there are some exceptions.
"Things like body lotions tend to thicken too much and are difficult to fill when they're cool, so we usually do those when they're still warm. Then there are things we have to fill hot, such as lip balms, so that has to be taken into account when you're doing the production scheduling."
After filling, the containers are capped and then placed in temporary storage.
When each batch is finished, the machines are stripped down and carefully cleaned before the next product can be started. Nicola's aim is to make about two to three products, with two filling sessions, per day.
To ensure each product is of consistent quality, a sample is kept of each batch for quality control. The Herb Farm doesn't use machine testing, preferring a more personal approach. "In testing we use all the senses. For a cream, the specifications are in terms of colour, consistency and smell. We try a bit on the skin and see that it rubs in the same way as previous batches."
Nicola checks this sample against a list of product specifications and can compare the new batch directly to previous samples. "It's all about consistency. Occasionally you might get a batch that comes out thicker than usual so we'd reject that batch to make sure that the customers have that consistency in every single product they are buying."
When the batch processing record is completed and signed off, the filled containers are taken through for labeling.

Nicky strongly identifies with the company ethos and enjoys the level of teamwork and pride in the job that all staff have. "We're all dedicated to making a difference. We talk about making our products with a positive intent, and I think that's the big difference between our products and similar ones on the market. It's actually written in our process instructions as well – when you're blending it for example, it actually says to blend it with positive intent, thinking about what its purpose will be. The manufacturing room is a lovely environment to work in, and I love going in there. So it's easy to walk through the storage area into the manufacturing area with the intent to make something special, that's going to make a difference to somebody."